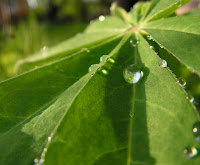
I am currently at the FMA Sustainability Conference in Florida and have been listening to 2 days of presentations about ways to be a more sustainable operation. Most of the audience would be described as executive level sustainability managers for Fortune 500 companies. After listening to these presentations, and giving one myself, it struck me that at the Mestek facility in Dallas we are actually pretty far down the road in implementing sustainable practices. For many, if not most, of the companies presenting or attending the conference the motivation was social responsibility with a by-product of reduced energy costs and improved financial performance. Our motivation was financial with the by-product being sustainability...but no matter what drives you the end result is the same. So, what has Dallas done to make us claim to be working in the direction of sustainability?
*All lighting was upgraded to high efficiency ballasts and high efficiency fixtures throughout the facility.
*Occupancy sensors are used to control lighting in areas that are not occupied at all times.
*The HVAC system is predominantly based on zero-GWP evaporative cooling. In areas that require mechanical cooling all of the systems have been converted to R410a from *R22 for reduced GHG impact.
*Our painting process is being changed from a solvent based system to a water based system to reduce VOCs.
*We have eliminated the need for one inefficient steam boiler in our coil testing area by changing our test procedure and by changing the cutting oil used in our production process to an oil that can be cleaned with water.
*We have eliminated the need for an auxiliary cooling system in our server room by enclosing the hot server exhaust stream and venting it outside the server room.
*All scrap metals are captured and sent to a recycling facility.
*Corrugated cardboard packaging is now being compressed to reduce the impact on the landfill.
*Each office has a paper products recycle bin and the material is consolidated weekly and sent to a recycling facility.
*80% of our customer training is now conducted by web-based conferencing...eliminating thousands of miles of air travel and the associated carbon footprint.
*All product literature is available in electronic form and only printed when necessary and in the amount required.
*IOM materials can be downloaded from the Internet by scanning a barcode tag on products shipped starting in late 2011...eliminating the need for multiple copies of thick manuals.
*Invoices, acknowledgments, and engineering submittals are all generated electronically...eliminating reams of paper consumption annually.
*E-mail has replaced fax as our preferred means of sharing printed documents.
All of these steps are items that have been covered during presentations here in Florida. In hindsight it turns out the Mestek Dallas is well along the road to sustainability...no matter the motivation.
No comments:
Post a Comment